The Role of Polyethylene Wax (PE WAX) in Cable Production
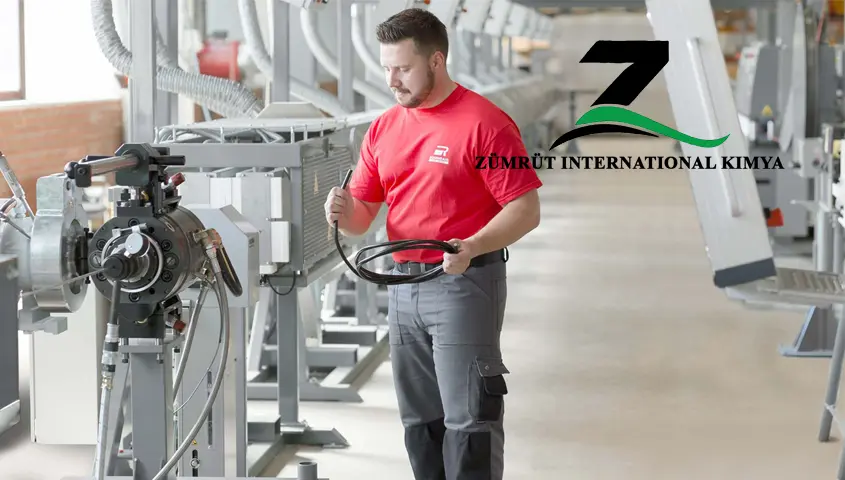
Introduction to PE Wax in Modern Cable Production
In an era where industries like telecommunications, energy, and electronics demand cables that are faster, safer, and more resilient, PE Wax (Polyethylene Wax) has emerged as a game-changing additive. This versatile polymer enhances processing efficiency, extends product lifespan, and aligns with sustainability goals, making it indispensable for manufacturers aiming to meet global standards. This comprehensive guide explores the critical role of Polyethylene wax in cable manufacturing, its applications, benefits, and environmental advantages, positioning it as a cornerstone of industrial innovation.
What is PE Wax?
Polyethylene Wax (PE Wax) is a low-molecular-weight polymer derived from ethylene. Renowned for its exceptional thermal stability, lubricity, and chemical resistance, PE Wax is a synthetic material widely used in plastics, coatings, and cable manufacturing. Its unique molecular structure allows it to act as a processing aid, dispersant, and performance enhancer, optimizing both production workflows and end-product quality.
Key properties of PE Wax
- High melting point (100°C–140°C) for thermal stability.
- Low viscosity for seamless integration into polymers.
- Hydrophobicity to repel moisture and prevent corrosion.
- Compatibility with PVC, polyethylene, and other polymers.
Application and Uses of PE Wax in the Cable Industry
1. Lubrication for Efficient Cable Extrusion
During extrusion, PE Wax reduces friction between molten polymers and machinery surfaces. This minimizes heat generation, prevents polymer degradation, and ensures smooth material flow. The result? Faster production speeds, reduced energy consumption, and lower operational costs.
2. Enhanced Surface Finish and Aesthetic Quality
Polyethylene wax delivers a glossy, uniform surface on cables, improving their aesthetic appeal while ensuring consistent insulation performance. This is vital for industries prioritizing both functionality and visual standards.
3. Uniform Dispersion of Additives
From flame retardants to UV stabilizers, Polyethylene wax ensures additives are evenly distributed within the polymer matrix. This homogeneity enhances cable performance in extreme conditions and maintains color consistency.
4. Thermal Stability for High-Temperature Environments
Cables exposed to heat during production or operation rely on Polyethylene wax to maintain structural integrity. Its heat-resistant properties prevent warping, cracking, and electrical failures.
5. Moisture and Chemical Resistance
For cables used underground or in humid environments, Polyethylene wax provides a protective barrier against water ingress, oxidation, and corrosive chemicals, significantly extending service life.
6. Improved Flexibility and Durability
By reducing internal stress during bending, PE Wax enhances cable flexibility without compromising tensile strength. This is critical for applications requiring frequent movement, such as robotics or automotive wiring.
Key Benefits of PE Wax for Cable Manufacturers
- Cost Efficiency: Reduces energy consumption, equipment wear, and downtime.
- Enhanced Performance: Boosts resistance to heat, moisture, and mechanical stress.
- Sustainability: Modern Polyethylene wax production uses recycled materials and eco-friendly processes.
- Versatility: Compatible with a wide range of polymers and manufacturing techniques.
Types of PE Wax for Industrial Cables
- Low-Density Polyethylene wax (LDPE): Ideal for flexible cables requiring smooth extrusion.
- High-Density Polyethylene wax (HDPE): Suited for heavy-duty cables in high-temperature settings.
- Oxidized Polyethylene wax (OPE): Enhances adhesion in coatings and polar polymer blends.
PE Wax and Sustainability: Aligning with Green Manufacturing
As industries prioritize eco-conscious practices, Polyethylene wax manufacturers are adopting sustainable innovations:
- Recycled Feedstocks: Using post-industrial polyethylene to reduce waste.
- Energy-Efficient Production: Lowering carbon footprints via advanced synthesis methods.
- Biodegradable Options: Research into bio-based PE Wax alternatives is ongoing.
This shift not only meets regulatory standards like REACH and RoHS but also appeals to environmentally responsible brands.
Why PE Wax is Essential for Next-Generation Cables
From 5G networks to renewable energy systems, modern infrastructure demands cables that perform reliably under stress. PE Wax addresses these needs by:
- Enabling thinner, lighter cable designs without sacrificing durability.
- Supporting high-speed data transmission in telecommunications.
- Withstanding extreme temperatures in power distribution grids.
FAQs About PE Wax in Cable Production
Q: Is PE Wax safe for use in electrical cables?
A: Absolutely. PE Wax is non-toxic, chemically inert, and compliant with international safety standards.
Q: How does PE Wax compare to paraffin wax?
A: PE Wax offers superior thermal stability and compatibility with polymers, making it more effective for high-performance cables.
Q: Can PE Wax be customized for specific applications?
A: Yes. Manufacturers can adjust molecular weight and oxidation levels to meet unique requirements.
Conclusion
PE Wax is more than an additive—it’s a strategic investment in efficiency, durability, and sustainability. By integrating high-quality Polyethylene Wax into your production process, you can meet evolving industry demands while reducing environmental impact.