Supplier of Acrylonitrile butadiene styrene
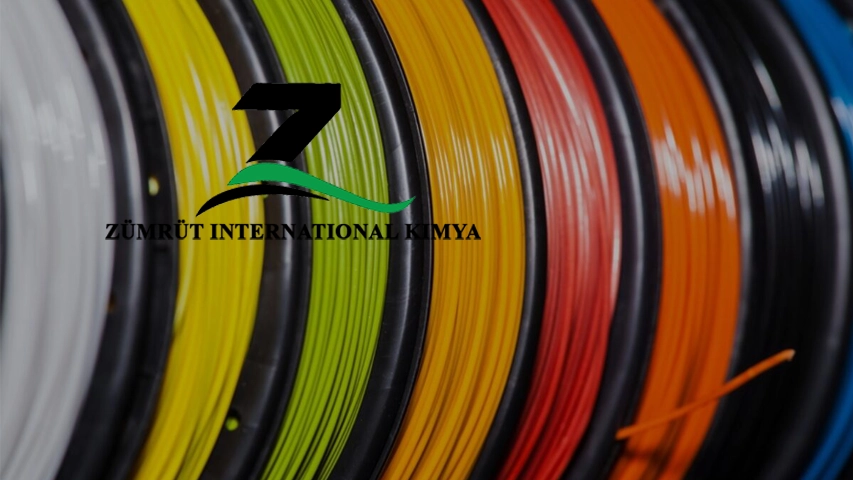
Introduction to Acrylonitrile Butadiene Styrene (ABS)
ABS is a hardy and resistant thermoplastic polymer with applications in numerous fields due to its great structural strength durability and versatility. ABS comprises three types of monomers, namely acrylonitrile, butadiene, and styrene. Each contributes different properties to ABS; thus, providing a lightweight yet strong plastic suitable for consumer and industrial purposes. Details about ABS characteristics, applications, and manufacturing processes will be explained in further sections.
What is ABS Made Of?
ABS is a copolymer primarily derived from three main monomers:
- Acrylonitrile – Provides rigidity and chemical resistance.
- Butadiene – Contributes to impact resistance and toughness.
- Styrene – Adds a glossy finish and enhances ease of processing.
All these combined monomers in one material compound give balanced rigidity, resistance to impact, and aesthetic appeal. Due to its structural versatility, ABS offers the opportunity to be engineered with specific properties, thus making it suitable for various industrial needs.
Properties of Acrylonitrile Butadiene Styrene (ABS)
ABS offers a unique combination of properties that make it a preferred choice in several applications. Here are some of the key properties that define ABS:
- High Impact Resistance: ABS is known for its toughness, which allows it to withstand sudden impacts without cracking or breaking, ideal for applications requiring durability.
- Good Thermal Stability: ABS performs well under moderate temperatures, typically between -20°C to 80°C, making it suitable for indoor and semi-outdoor applications.
- Chemical Resistance: The presence of acrylonitrile enhances ABS’s resistance to chemicals, oils, and various solvents, increasing its versatility.
- Ease of Processing: With a relatively low melting point of 105°C, ABS can be easily molded into complex shapes, reducing manufacturing costs and time.
- Aesthetic Finishing: The styrene component of ABS provides a glossy surface that makes the material suitable for products requiring an attractive finish.
These properties make ABS a popular material in applications ranging from consumer electronics to automotive parts.
Applications and Uses of ABS
ABS is widely used in multiple industries, including automotive, electronics, household appliances, and construction. Here are some of the main applications:
- Automotive Industry: ABS also finds extensive use in car interiors, making dashboards, and bumpers owing to its very high resistance to impact and toughness. It is inexpensive and efficient in molding, hence very suitable for use in the manufacture of complex automotive parts.
- Consumer Electronics: In electronics, ABS is utilized in manufacturing cases for computers, televisions, and telecommunication devices. Its aesthetic appeal, along with thermal stability, makes it suitable for electronic housings and components.
- Household Goods and Appliances: Many household items such as vacuum cleaners, kitchen appliances, and toys are manufactured using ABS. Its glossy finish and toughness are advantageous in products subject to frequent use.
- Construction and Plumbing: ABS pipes are widely used for drainage systems due to their durability and chemical resistance, which can withstand various environmental factors.
- 3D Printing: ABS is one of the most used materials in 3D printing, above all in the prototyping of products and in basic industrial use. With easy printing and a smooth finish, it will enable the making of detailed resistant models.
Production Process of ABS
The production of ABS involves a combination of polymerization and emulsion processes. Here is a general overview of how ABS is manufactured:
- Polymerization of Acrylonitrile and Styrene: The acrylonitrile and styrene monomers are first polymerized, creating a base polymer.
- Addition of Butadiene: To this polymerized mixture of acrylonitrile and styrene, butadiene rubber particles are normally added in an emulsion so that there is a uniform dispersion of the rubber particles in a polymer matrix.
- Emulsion Polymerization: Emulsion polymerization is preferred for ABS production since this allows good control of the molecular weight and distribution of the rubber particles to achieve the desired level of impact resistance and rigidity.
- Extrusion and Pelletizing: The ABS material, after polymerization, is extruded and then cooled down. It is then made into pellets for easy transportation to further processing. Pellets are then shipped out to manufacturers who mold them into final products.
Environmental and Safety Considerations for ABS
ABS is generally considered safe for most applications and does not contain any known toxic components. However, during its production and end-of-life disposal, certain environmental considerations are necessary:
- Recyclability: ABS is recyclable, which helps mitigate its environmental impact. Recycled ABS can be used in various applications, although it may not have the same quality as virgin ABS.
- Combustibility: ABS is flammable and can emit toxic fumes when burned. Therefore, products made from ABS should be used with caution in high-temperature environments.
- Disposal: ABS should be disposed of properly to minimize environmental pollution. Recycling programs for ABS products are increasingly available, allowing for a more sustainable lifecycle.
Packaging of ABS Products
ABS usually comes in pellet form and is, therefore, fairly easy to transport and handle. Pellets are stored in moisture-resistant bags or containers that prevent contamination and are shipped en masse to manufacturing facilities. In some applications that may require colored or treated ABS, the pellets are mixed with certain additives or colorants before being packaged.
Conclusion
ABS is a singular, diversified methodology that can meet a great many needs cost-effectively. The excellent resistance to impact, durability, and ease with which ABS is processed have given this material a foothold in everything from automotive and electronics to construction and 3D printing. Besides, as manufacturers and consumers alike turn greener, ABS recycling programs and innovations that correspond to this trend can only continue their upward trend, perhaps positioning this amazing polymer to play a significant role in sustaining the future.
For inquiries or more information on ABS, feel free to contact ZÜMRÜT International Kimya Co., your trusted partner in chemical solutions and polymer innovations.
Read About Polystyrene (Click)