Supplier of Medium-density polyethylene (MDPE)
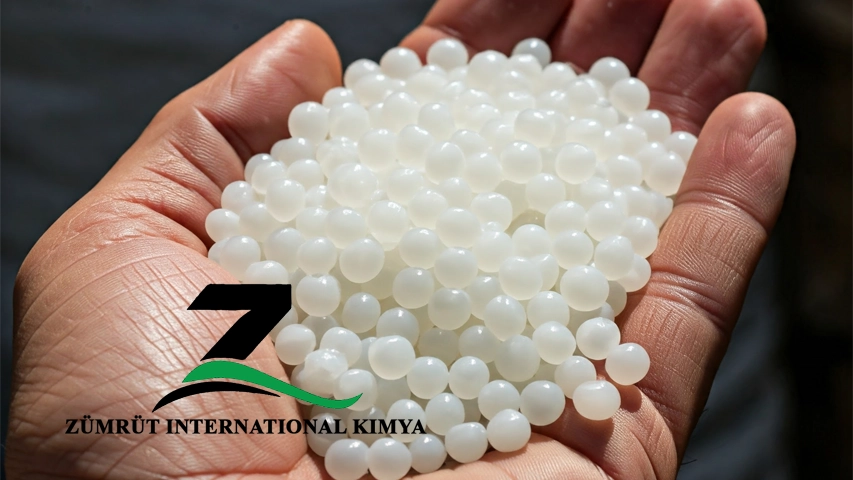
Introduction of MDPE
Medium-Density Polyethylene (MDPE) is a versatile, semi-flexible polymer known for its unique balance of properties. Its intermediate density, situated between high-density polyethylene (HDPE) and low-density polyethylene (LDPE), makes it a preferred choice in water and gas packaging, construction, and piping systems. Combining strength, flexibility, and impact resistance, MDPE addresses diverse industrial needs efficiently. This article deals with properties, grades, production processes, applications, and packaging considerations of MDPE. It gives an all-around understanding of the industries that are in pursuit of leveraging the benefits of MDPE for sustainability and enhanced value.
What is Medium-Density Polyethylene (MDPE)?
Medium-density polyethylene (MDPE) is a thermoplastic polymer derived from the polymerization of ethylene gas. With a density range of 0.926 to 0.940 g/cm³, MDPE offers a balance of flexibility and toughness, making it highly adaptable to various applications. Compared to LDPE, MDPE exhibits greater impact resistance while being more flexible than HDPE. Its molecular structure enhances crack resistance, ensuring durability even under challenging conditions, such as extreme temperatures or environmental stress.
Key Properties of Medium-Density Polyethylene
- Impact Resistance: MDPE exhibits strong impact resistance, especially at low temperatures, making it a prime material for applications that face harsh environmental conditions.
- Chemical Resistance: With MDPE, good chemical resistance is maintained because it does not degrade from most solvents, acids, and bases matter of reliance for containers or pipelines in industries dealing with chemicals and agriculture.
- Flexibility and Toughness: The balance between flexibility and rigidity in MDPE helps it withstand physical stress, a feature critical in pipes and fittings.
- UV Stability: MDPE can be enhanced with UV stabilizers, allowing it to resist degradation from prolonged exposure to sunlight, which is essential for outdoor applications.
- Thermal Stability: MDPE has a fair range of thermal stability. It can be used in moderate-temperature applications but does not perform well under extreme heat.
Various Grades of Medium-Density Polyethylene (MDPE)
MDPE is available in multiple grades tailored to different applications. Each grade varies in terms of density, melt flow rate, and additional characteristics:
General Purpose MDPE:
- This grade represents a versatile choice for everyday applications. It commonly finds its way into the production of packaging films, consumer goods, and general-purpose plastic components. Its blend of moderate strength and flexibility renders it ideal for items that have to be tough yet easy to handle.
Pipe-grade MDPE:
- Pipe-grade MDPE is engineered specifically for gas and water pipeline systems. It is known for its exceptional impact resistance and environmental stress-crack resistance, ensuring long-term durability even under high-pressure conditions. Additionally, it is enhanced with UV stabilizers, allowing it to withstand prolonged outdoor exposure without degradation. This grade is widely recognized for its reliability in municipal infrastructure projects and industrial piping networks.
Rotomolding MDPE:
- Rotomolding MDPE is optimized for rotational molding applications, making it a preferred choice for creating large, hollow, and seamless structures. Common products include water storage tanks, industrial containers, and playground equipment. This grade’s ease of processing, combined with its excellent impact resistance and flexibility, ensures consistent quality across a range of complex designs.
Injection Molding Grade MDPE:
- MDPE injection molding, specially formulated for precision applications, is used to manufacture caps, closures, small fittings, and automotive components. Its excellent flow properties during molding ensure smooth finishes and accurate dimensions, which are critical in many industries that require high-quality output.
Blown Film Grade MDPE:
- Blown film MDPE is specifically developed for the production of thin and tough plastic films. These are commonly utilized in agricultural applications, industrial wraps, and food packaging. The high tear resistance and good flexibility of this grade ensure optimal performance in conditions where puncture resistance and protection against moisture are essential.
Each grade of MDPE is engineered with specific applications in mind, allowing manufacturers to choose a variant that precisely meets their product requirements.
Application and Uses of MDPE
Piping Systems:
- MDPE’s resistance to environmental stress cracking and its durability under physical stress make it the preferred material for gas and water pipelines. The flexibility of the material makes it easier to install in-ground movement areas, while the resistance to corrosion and chemical damage provides a long lifespan. MDPE pipes are quite effective in urban utility networks, irrigation systems, and industrial transport systems.
Packaging Materials:
- MDPE is a critical packaging product in the industry for any product to ensure strength and moisture resistance. Its applications extend to shrink wraps, stretch films, and agricultural films, which protect goods with their durability. More importantly, it is food-grade, thereby suitable for packaging consumable goods safely and reliably to prevent contamination.
Chemical Containers and Storage Tanks:
- The high chemical resistance and toughness of MDPE make it an ideal material for manufacturing storage tanks-chemical, fuel, and other corrosive substances. It is light in weight too. So, the installation process becomes less complicated in comparison to metal materials.
Consumer Products:
- MDPE is used in all sorts of consumer products, such as toys and outdoor furniture, garden equipment, and even household appliances. Its UV exposure and varying weather conditions ensure the quality of such products.
Construction Materials:
- In construction, MDPE is used for insulation, vapor barriers, drainage systems, and foundation coatings. The durability and environmental stress resistance of MDPE makes constructions last longer, making it a relatively low-cost solution for modern building projects.
Agricultural Applications
- Farmers and agricultural enterprises use MDPE films and pipes in irrigation systems, covering greenhouses, and in silage bags. Chemical resistance, resistance to tearing, and easy handling make the material indispensable in agriculture.
Production Process of Medium-Density Polyethylene
The production of MDPE is a highly controlled process that can be achieved via two main methods:
- Gas-Phase Polymerization: Most of the ethylene gas is polymerized in a fluidized bed reactor at controlled pressure. Controlled pressure is generally achieved with the use of Ziegler-Natta or chromium catalysts, which afford precise control over molecular weight and branching of the polymer: key to attaining the specific density and flexibility that is characteristic of MDPE.
- Solution Polymerization: This requires that ethylene be first dissolved in a solvent and then polymerized at high temperature and pressure. Solution polymerization works best to develop MDPE grades whose molecular structure is much more uniform and, for this reason, is usually favored in the manufacture of quality grades of MDPE for special uses.
Some additives, such as UV resistance, heat stability, and extra toughness, can be included in the production phase of MDPE to improve such properties for the final product application and requirements.
Packaging of Medium-Density Polyethylene
Proper packaging of MDPE is essential for maintaining product quality and ensuring safe transport and storage:
- Moisture Protection: MDPE should be stored in moisture-proof packaging to prevent any potential degradation. Bags made from polyethylene or lined containers are suitable for this purpose.
- UV Protection: MDPE products intended for outdoor storage should be packaged in UV-protective materials or stored in shaded areas to prevent exposure to sunlight.
- Temperature Control: While there is a degree of temperature resistance with MDPE, storage conditions should not be allowed to exceed 35°C (95°F), providing that material integrity is the issue at hand. Excessive heat could lead to degradation sooner than expected, particularly in thinner films and sheets of MDPE.
Conclusion
Medium-density polyethylene stands as one of the most valuable varieties of polymers because of its special features, answering many various needs in the industry. The different classes of MDPE grades, each suited for specific uses, give manufacturers a leeway to choose an ideal variant that suits their needs. From piping systems and packaging through construction, its balanced properties of resistance against wear and tear, flexibility, and impact resistance make MDPE a vital material in consumer and industrial products. With the innovations taking place within industries, the role of MDPE keeps on expanding its position as a reliable and versatile polymer within world markets.