The Role Of Linear Low-Density Polyethylene (LLDPE) in Injection Molding
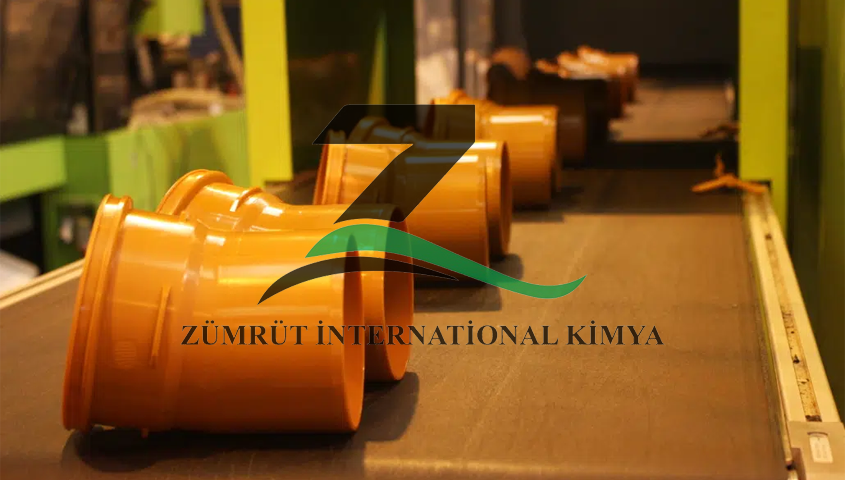
Introduction
Linear Low-Density Polyethylene (LLDPE) is an extremely versatile thermoplastic with wide usage in general industrial applications. Injection molding also falls into its important category since the specific nature of its properties makes it quite indispensable for such product lines in developing high-quality, enduring products.
What is LLDPE?
Linear Low-Density Polyethylene, or LLDPE for short, belongs to the family of polyethylenes, characterized by its linear molecular configuration with considerable short-chain branching. This gives LLDPE a singular combination of flexibility, strength, and resistance to environmental stress cracking. Whereas HDPE is very rigid, LLDPE is much more resistant to impact and has much better toughness, which makes it perfect for those products that need a lot of durability.
Key Properties of LLDPE in Injection Molding
LLDPE exhibits several properties that make it suitable for injection molding:
- High Impact Resistance: LLDPE’s exceptional toughness allows it to absorb impacts without breaking, which is essential for many molded products.
- Flexibility: Its flexibility makes it ideal for creating products that require some degree of elasticity.
- Chemical Resistance: LLDPE offers excellent resistance to chemicals and solvents, ensuring durability in harsh environments.
- Low Melting Point: With a relatively low melting point, LLDPE enables efficient and energy-saving molding processes.
- Lightweight: Products made from LLDPE are lightweight yet durable, meeting the requirements of industries seeking cost-effective solutions.
Benefits of Using LLDPE in Injection Molding
Using LLDPE in injection molding brings a range of advantages:
Design Versatility:
- This property of LLDPE permits the creation of very intricate and accurate designs because of its good flow characteristics that help it to distribute uniformly in the mold, thereby increasing the quality of the molded components.
Cost-Effectiveness:
- The low density and lightweight nature of LLDPE reduce material consumption and shipping costs. Besides, its relatively cheapness compared to other polymers makes the material economically viable for large-scale production.
Process Efficiency:
- The low melting point of LLDPE speeds up the injection molding process, reducing energy costs and increasing production rates. This efficiency enables manufacturers to meet tight deadlines without compromising product quality.
Recyclability:
- LLDPE is recyclable, hence allowing environmentally sensitive producers to use it. It makes companies go greener by infusing recycled materials into their product cycle since going green has become a topic of discussion around the world.
Applications of LLDPE in Injection Molding
Linear low-density polyethylene is slowly becoming the single most important general injection molding material, finding applications that range through many different industries where a strong, resilient, and value-for-money solution is required. Applications include:
Consumer Goods
- The most common uses of LLDPE in household consumption industries are because the material is light, resistant to impact, and flexible. It is applied in the making of food storage utensils, lid utensils, waste bins, and household tooling. Moreover, the material is wear-resistant, and thus products made from the material can be long-lasting, although they are used daily. Its cost-effectiveness is another aspect that makes it suitable for most high-volume consumer goods.
Packaging Industry
- The packaging industry relies greatly on LLDPE for flexible food-grade container pack and beverage bottle packaging. Due to its high chemical resistance, LLDPE has been able to maintain packaged items contamination-free, safe for a prolonged period, and fresh. Packaging solutions such as caps and closures in injection molding packaging have inbuilt material potential for tight sealing and moisture barrier that prolongs the shelf life of products. LLDPE is therefore a preferred choice for food-grade packages as well as industrial packages.
Agriculture Applications
- In agriculture, LLDPE is used for the manufacture of hard and flexible products such as irrigation pipes, fittings, and tools. All these products have to withstand very harsh conditions: UV, temperature fluctuations, and water. The stress-cracking resistance and toughness of LLDPE make the material particularly ideal for such use, leading to agricultural machinery running continuously over a long period. Apart from that, its affordability leads to the establishment of relatively low-cost solutions for farmers worldwide.
Industrial Parts
- LLDPE in manufacturing is used in the production of injection-molded parts, for instance, fittings for pipes, seals, and protective caps. As a result of its high impact resistance, these parts will withstand the most severe conditions of operation, such as severe mechanical loads and aggressive chemical environments. Besides that, LLDPE maintains its properties over a wide range of temperatures and is applied in factories and chemical processing, among other industrial manufacturing sectors. Its recyclability provides sustainability in industrial manufacturing.
Optimizing LLDPE for Injection Molding
The best result in injection molding with LLDPE is obtained by optimizing parameters like pressure, temperature, and cooling time. Besides that, good mold design and proper material choice become extremely important as regards quality output. There is a possibility of enhancing properties for specific applications by blending LLDPE with other polymers or additives.
Conclusion
LLDPE is a very adaptable resin; thus, it has excellent properties and benefits that make it well-suited for injection molding. From cost-effectiveness to durability, LLDPE lets manufacturers reliably produce quality products in an environmentally sustainable manner. LLDPE remains the mainstay of modern injection molding as industries move into more innovative manufacturing, serving almost every sector in the world.