Supplier of Polyethylene Wax (PE-WAX) from Turkey and Dubai-UAE
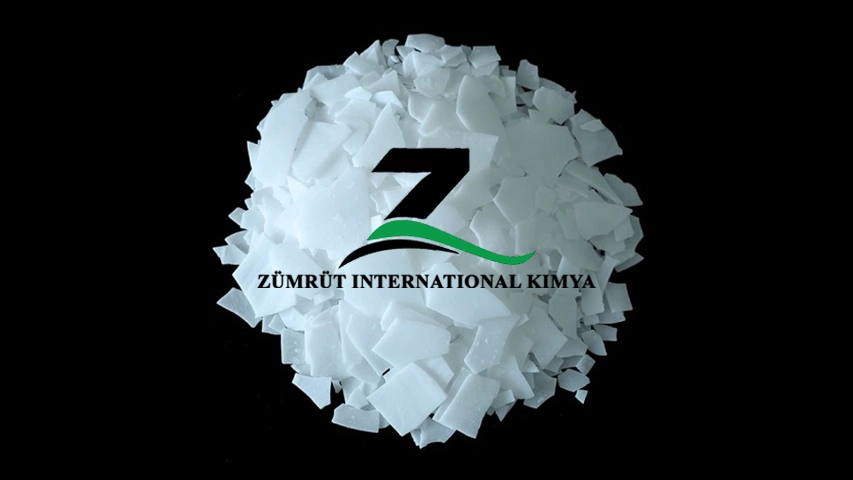
Introduction
Polyethylene wax, commonly known as PE wax, is a versatile, ultra-low molecular weight polyethylene used across industries for its unique properties. As a leading supplier of PE wax, ZÜMRÜT International Kimya Co. provides high-quality polyethylene wax tailored to your needs. In this guide, we’ll explore what PE wax is, its applications, benefits, production methods, and how to choose a reliable polyethylene wax supplier like ZÜMRÜT International Kimya Co.
What is Polyethylene Wax?
PE wax is a low molecular weight polymer derived from ethylene, known for its low viscosity, high thermal stability, and excellent compatibility with other materials. Available in high-density (HDPE) and low-density (LDPE) forms, it comes in various grades to suit specific applications. Whether you’re in plastics, coatings, or adhesives, partnering with a trusted supplier of polyethylene wax ensures consistent quality and performance.
Applications of Polyethylene Wax
PE wax is a powerhouse material used in multiple industries due to its multifunctional properties. Here are its key applications:
-
Plastic Processing: PE wax acts as a lubricant and mold release agent, improving flow during molding and delivering flawless finishes in plastic products like bottles and packaging.
-
Coatings and Inks: As a PE wax supplier, we provide wax that enhances durability, scratch resistance, and surface quality in coatings and printing inks, ideal for industrial and decorative applications.
-
Rubber Processing: PE wax reduces friction and ensures uniform dispersion of additives in rubber compounding, resulting in high-performance tires and industrial rubber products.
-
Cosmetic Formulations: Valued for its emollient properties, PE wax creates smooth textures in lipsticks, creams, and lotions, enhancing product appeal.
-
Adhesives: PE wax improves flow, tack, and adhesion in hot-melt adhesives, optimizing performance in packaging and construction.
-
Cable and Wire Manufacturing: As a slip agent, PE wax ensures smoother extrusion and better insulation integrity in cables and wires.
-
Paper and Packaging: PE wax enhances water resistance and surface finish in paper coatings and packaging films, ensuring durability and a premium look.
How is PE Wax Made?
Polyethylene wax is produced through several methods, each designed to achieve specific molecular weights and properties:
-
Direct Polymerization: Ethylene is polymerized under controlled conditions to create low molecular weight PE wax with precise characteristics.
-
Thermal Degradation: High molecular weight polyethylene is broken down into lower molecular weight fractions, ideal for producing consistent wax grades.
-
Fraction Separation: Low molecular weight fractions are separated from high molecular weight polymers, yielding high-purity PE wax.
As a polyethylene wax manufacturer, ZÜMRÜT International Kimya Co. uses advanced production techniques to deliver reliable, high-quality wax for your industry needs.
Types and Grades of PE Wax
PE wax varies based on three key characteristics: molecular weight, degree of polymer branching, and monomer composition. These factors influence viscosity, hardness, and melting point.
Types of PE Wax
-
Conventional PE Wax: A standard option for plastics, coatings, and adhesives, offering reliable performance.
-
Functionalized PE Wax: Chemically modified for enhanced compatibility with specific polymers, ideal for specialized formulations.
Grades of PE Wax
-
Low Molecular Weight: Provides excellent flow and reduced viscosity, perfect for efficient processing in plastics and coatings.
-
High Molecular Weight: Offers superior structural integrity and higher melting points for durable applications like heavy-duty coatings.
-
Specialty Grades: Tailored for niche uses, these grades feature enhanced thermal stability and adhesion for demanding environments.
Advantages of Using PE Wax
Partnering with a trusted supplier of PE wax, like ZÜMRÜT International Kimya Co., unlocks numerous benefits:
-
Improved Processing: Low viscosity enhances polymer flow, reducing energy consumption and production time.
-
Superior Finish: PE wax delivers glossy, durable surfaces in plastics, coatings, and packaging.
-
Cost Efficiency: Reduces the need for multiple additives, lowering production costs.
-
Thermal Stability: Withstands high temperatures, making it ideal for heat-sensitive applications.
-
Eco-Friendly Options: Refined production methods offer environmentally friendly PE wax grades.
-
Lubrication for PVC: As an external lubricant, PE wax enhances extrusion capacity and imparts a shiny finish to PVC products without altering color due to its oxidation resistance.
-
Food-Safe Applications: Non-toxic PE wax is suitable for food packaging, meeting strict safety standards.
Packaging Options for PE Wax
At ZÜMRÜT International Kimya Co., we ensure our PE wax is packaged to maintain quality and meet customer needs:
-
25 kg PP Bags: Prevents moisture absorption, ensuring product integrity.
-
Jumbo Bags: Ideal for bulk orders, with PP bags placed inside for added protection.
-
Custom Packaging: Options include PP bags on pallets with shrink wrap or in jumbo bags, tailored to your requirements.
Why Choose ZÜMRÜT International Kimya Co. as Your PE Wax Supplier?
Selecting the right PE wax supplier is crucial for your business. ZÜMRÜT International Kimya Co. stands out due to:
-
High-Quality Products: We offer a range of PE wax grades tailored to your industry.
-
Reliable Supply Chain: Our global network ensures timely delivery to keep your operations running smoothly.
-
Expert Support: Our team provides technical guidance to optimize PE wax use in your applications.
-
Competitive Pricing: We deliver cost-effective solutions without compromising quality.
Frequently Asked Questions
We offer high-quality PE wax, reliable global delivery, competitive prices, and expert technical support, ensuring your business gets the best value and performance.
The right grade depends on your application — low molecular weight for flow, high molecular weight for durability, or specialty grades for specific needs. Contact us for expert advice.
PE wax is made through direct polymerization of ethylene, thermal degradation of polyethylene, or fraction separation, each method producing specific grades with unique properties.
Yes, polyethylene wax is non-toxic and meets food safety standards, making it suitable for use in food contact applications like packaging films and coatings.
Polyethylene wax is used in plastics, coatings, adhesives, rubber, cosmetics, cables, and packaging as a lubricant, dispersing agent, and surface enhancer due to its excellent thermal stability and low viscosity.
Contact Us for Your PE Wax Needs
Ready to source high-quality polyethylene wax? ZÜMRÜT International Kimya Co. is your trusted supplier of PE wax. Contact us today to discuss your requirements or request a quote:
-
📞 Phone/WhatsApp: +971 50 720 9246
-
📧 Email: info@causticsodaco.com
-
🌐 Website: www.causticsodaco.com