Polyethylene Wax Flakes Supplier from Turkey and Dubai UAE
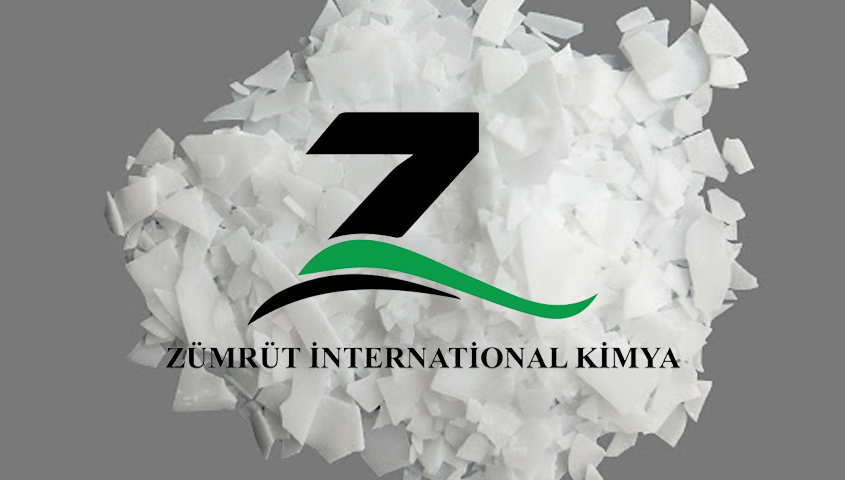
Introduction
Polyethylene wax (PE wax) is a high-performance polymer widely used in various industrial applications due to its excellent lubrication, thermal stability, and chemical resistance. Among its different forms, PE wax flakes are particularly valued for their ease of handling, storage, and incorporation into formulations. This article explores the properties, applications, and benefits of polyethylene wax flakes, emphasizing their importance in multiple industries.
Properties of Polyethylene Wax Flakes
PE Wax flakes are synthesized via polymerization or thermal cracking of polyethylene, yielding a material with unique characteristics:
- High Thermal Stability: Withstand extreme temperatures without degradation, ideal for high-heat applications like plastic extrusion.
- Superior Lubrication: Reduce friction in processing equipment, enhancing efficiency in plastics, rubber, and coatings production.
- Chemical Resistance: Resist acids, alkalis, and solvents, ensuring durability in harsh environments.
- Low Viscosity: Enable easy dispersion in coatings, inks, and adhesives for smooth application.
- Hydrophobicity: Provide water-repellent properties for moisture-resistant coatings and textiles.
These properties make PE wax flakes a top choice for manufacturers prioritizing performance and cost-effectiveness.
Grades of Polyethylene Wax
Polyethylene wax is categorized into several grades based on production methods, molecular weight, and functional properties:
1. High-Density Polyethylene Wax (HDPE Wax)
- Production: Derived from high-density polyethylene (HDPE) through controlled degradation or direct polymerization.
-
Properties:
- High melting point (110°C–140°C).
- Superior hardness and rigidity.
- Excellent thermal stability.
-
Applications:
- Lubricant for PVC and engineering plastics.
- Processing aid in high-temperature extrusion.
- Additive for rigid coatings and masterbatches.
2. Low-Density Polyethylene Wax (LDPE Wax)
- Production: Created from low-density polyethylene (LDPE) via thermal cracking.
-
Properties:
- Lower melting point (90°C–110°C).
- Flexible and less brittle than HDPE wax.
- Good compatibility with elastomers.
-
Applications:
- Dispersing agent in inks and paints.
- Candle manufacturing for improved texture.
- Additive in hot-melt adhesives.
3. Oxidized Polyethylene Wax
- Production: Treated with oxygen to introduce polar functional groups.
- Properties:
- Enhanced compatibility with polar materials (e.g., coatings, resins).
- Improved emulsification and adhesion.
- Melting point: 100°C–130°C.
- Applications:
- Key components in polishes, floor coatings, and crayons.
- Lubricant for PVC pipe production.
- Waterproofing agent in textiles.
4. Micronized Polyethylene Wax
- Production: Finely ground into micron-sized particles for uniform dispersion.
- Properties:
- Ultra-fine particle size (5–30 microns).
- High surface area for better performance at lower dosages.
- Applications:
- Matte finish additive in automotive coatings.
- Anti-blocking agent in plastic films.
- Enhancer for printing ink rub resistance.
5. Fischer-Tropsch Polyethylene Wax
- Production: Synthesized via the Fischer-Tropsch process from natural gas or coal.
- Properties:
- Narrow molecular weight distribution.
- High purity and whiteness.
- Melting point: 100°C–120°C.
- Applications:
- Cosmetics (e.g., lipsticks, creams).
- Food-grade packaging coatings.
- Precision mold release agents.
How to Choose the Right Grade of Polyethylene Wax
- Process Temperature: Select HDPE wax for high-heat applications (>120°C).
- Polarity: Use oxidized PE wax for coatings or adhesives requiring polar compatibility.
- Particle Size: Opt for micronized grades in fine coatings or inks.
- Regulatory Compliance: Fischer-Tropsch wax is ideal for food-safe or cosmetic uses.
Applications of Polyethylene Wax Flakes
PE wax flakes are widely utilized in numerous industries due to their exceptional physical and chemical characteristics. Some of the primary applications include:
Plastic and Rubber Processing
- In the plastic industry, polyethylene wax flakes act as an internal and external lubricant, improving melt flow and preventing adhesion to processing equipment. In rubber processing, they enhance the dispersion of fillers and reduce tackiness, improving product performance.
Coatings and Paints
- PE wax flakes are used in coatings and paints to improve surface properties such as scratch resistance, gloss control, and anti-blocking. Their low viscosity ensures uniform dispersion in formulations, enhancing durability and water repellency.
Printing Inks
- PE wax flakes serve as an essential additive in printing inks, where they enhance rub resistance, gloss, and pigment dispersion. Their low melting point enables smooth application, ensuring high-quality prints.
Adhesives and Sealants
- As a key component in adhesives, PE wax flakes enhance viscosity control and increase bond strength. Their chemical stability and water repellency make them suitable for high-performance adhesives used in packaging, woodworking, and automotive industries.
Textile and Leather Treatment
- In the textile and leather industry, PE wax flakes are applied as finishing agents to impart softness, water repellency, and abrasion resistance. They enhance the durability and aesthetic appeal of fabrics and leather products.
Benefits of Using Polyethylene Wax Flakes
Enhanced Manufacturing Efficiency
- Reduce friction and equipment wear, lowering maintenance costs.
- Improve processing speed with easy blending and dispersion.
Superior Product Performance
- Boost thermal stability and surface smoothness in end products.
- Enhance scratch resistance in coatings and rub resistance in inks.
Cost Savings
- High efficiency at low usage rates reduces raw material expenses.
- Minimize waste and improve production yield.
Sustainability
- Eco-friendly formulations align with global regulations.
- Biodegradable options support green manufacturing initiatives.
Why Choose Polyethylene Wax Flakes?
PE wax flakes offer unmatched versatility for industries seeking to optimize performance while reducing costs. Their compatibility with diverse materials and eco-friendly profiles make them a future-proof solution.
Conclusion
Polyethylene wax (PE wax) flakes are a versatile and high-performance material with applications across plastics, coatings, inks, adhesives, and textiles. Their exceptional properties, including lubrication, chemical resistance, and thermal stability, make them indispensable in numerous industries. As demand for high-quality industrial additives continues to grow, polyethylene wax flakes remain a key component in optimizing product performance and manufacturing efficiency.
For premium-quality polyethylene wax flakes, contact Zumrut International Kimya today.