Supplier of Styrene-Butadiene Rubber (SBR)
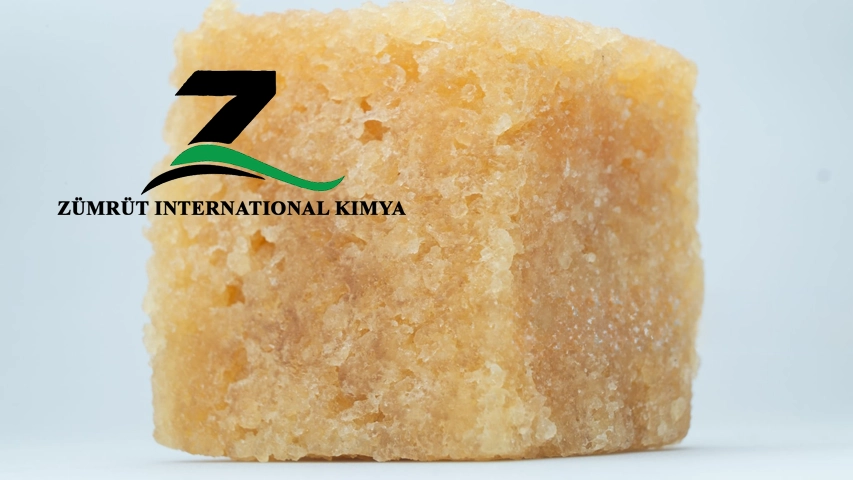
Your Trusted Partner for High-Quality Synthetic Rubber Solutions
At ZÜMRÜT International Kimya Co., we take pride in being a leading Styrene Butadiene Rubber (SBR) supplier and exporter, delivering premium synthetic rubber to manufacturers, distributors, and industrial clients worldwide.
Our mission is simple — to provide consistent quality, competitive pricing, and on-time delivery of SBR that meets the demanding needs of industries such as automotive, construction, manufacturing, adhesives, footwear, and more. Whether you require bulk shipments or specialized grades, we have the expertise and resources to deliver exactly what your business needs. (Contact Us)
What is Styrene Butadiene Rubber (SBR)?
Styrene Butadiene Rubber is a high-performance synthetic elastomer made from styrene and butadiene monomers. Known for its durability, abrasion resistance, and flexibility, SBR has become one of the most widely used rubbers in the world. It offers a cost-effective alternative to natural rubber while delivering consistent performance in various applications.
At ZÜMRÜT International Kimya Co., we source and supply only top-grade SBR from reliable producers, ensuring every shipment meets strict international quality standards.
Key Advantages of SBR
-
Exceptional Abrasion Resistance – Perfect for tire treads, conveyor belts, and heavy-duty applications.
-
Long-Term Performance – Resistant to aging, cracking, and environmental wear.
-
Superior Flexibility & Strength – Maintains integrity under stress and varying conditions.
-
Cost-Effective Alternative – Lower production costs without sacrificing quality.
-
Wide Industrial Usability – Suitable for multiple sectors, from automotive to consumer goods.
Applications of SBR We Supply
Automotive Industry
-
Tire manufacturing (treads, sidewalls, and inner linings)
-
Engine seals, gaskets, and hoses
-
Vibration and shock absorption components
Industrial & Manufacturing
-
Conveyor belts and flooring systems
-
Rubberized coatings and protective layers
-
Heavy-duty gaskets and vibration dampeners
Construction Sector
-
Waterproof membranes
-
Flexible sealants and adhesives
-
Bonding agents for construction materials
Consumer & Everyday Products
-
Footwear soles and sports equipment
-
Household rubber products
-
Durable rubberized coatings
Types of SBR We Offer
-
E-SBR (Emulsion Polymerized SBR) – General-purpose and oil-extended grades for versatility.
-
S-SBR (Solution Polymerized SBR) – Superior molecular control for eco-friendly tires and advanced applications.
-
Cold Polymerized SBR – Higher tensile strength and resilience.
-
Carboxylated SBR (XSBR) – Enhanced adhesion for coatings and adhesives.
-
Latex SBR – Ideal for carpet backing, paper coatings, and adhesives.
-
Oil-Extended SBR – Improved processing and reduced costs for tire manufacturing.
Our Packaging Solutions
-
Bales – Wrapped for cleanliness and easy handling.
-
Pellets – Efficient storage and processing.
-
Bulk Containers – For large-scale industrial orders.
We tailor packaging to meet your specific logistics and storage requirements, ensuring efficiency from factory to final delivery.
Why Partner with ZÜMRÜT International Kimya Co.?
-
Global Supply Network – Reliable access to high-quality SBR in multiple grades.
-
Competitive Pricing – Transparent rates aligned with market conditions.
-
Strict Quality Control – Products meet or exceed international standards.
-
On-Time Delivery – Robust logistics for global shipments.
-
Customer-Focused Service – Personalized solutions for every client.
When you work with us, you don’t just buy SBR — you secure a reliable supply chain partner who understands your industry.
Contact Us – Your Global SBR Supplier
📞 Phone/WhatsApp: +971 50 720 9246
📧 Email: info@causticsodaco.com
🌐 Website: www.causticsodaco.com
ZÜMRÜT International Kimya Co. — Supplying Styrene Butadiene Rubber (SBR) with quality, reliability, and professionalism you can count on. (Contact Us)