Supplier of High density polyethylene (HDPE) from Turkey and Dubai UAE
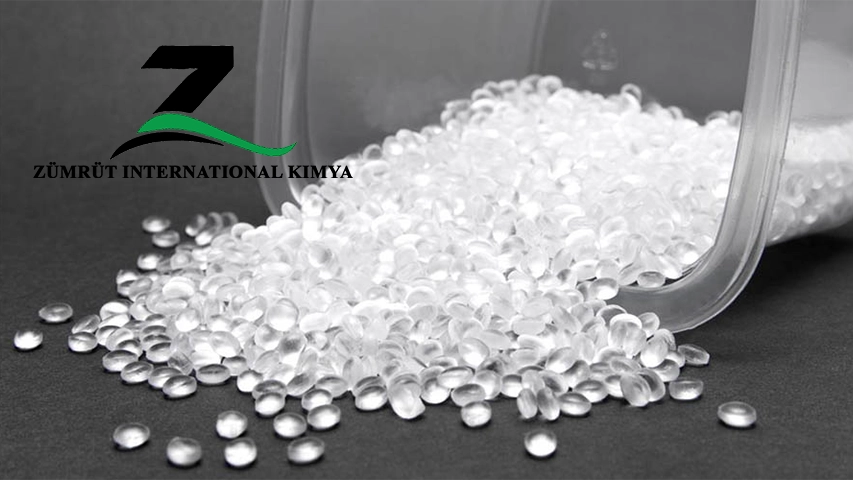
Introduction
As a premier supplier of HDPE, ZÜMRÜT International Kimya Co. delivers high-quality High-Density Polyethylene (HDPE) to industries worldwide. Specializing in durable, sustainable HDPE materials, we cater to packaging, construction, automotive, and healthcare sectors. Our HDPE solutions meet ASTM D4976 and ISO 9001 standards, ensuring reliability and performance. Discover why ZÜMRÜT is the leading HDPE supplier for your business needs.
What is High-Density Polyethylene (HDPE)?
High-Density Polyethylene (HDPE) is a versatile thermoplastic polymer known for its high strength-to-density ratio, making it ideal for demanding applications. Derived from petroleum, HDPE’s tightly packed molecular structure provides exceptional durability, impact resistance, and moisture impermeability. As a #2 recyclable plastic, HDPE supports sustainability, making ZÜMRÜT a preferred polyethylene supplier for eco-conscious businesses.
As a global supplier of HDPE, we offer HDPE in various forms—pellets, sheets, pipes, and films—customized to meet your project requirements. Whether you need HDPE pellets for injection molding or HDPE pipes for infrastructure, our materials deliver unmatched quality.
Key Properties of HDPE
ZÜMRÜT, a trusted HDPE manufacturer and supplier, ensures our materials offer:
- High Strength-to-Density Ratio: Lightweight yet robust, ideal for heavy-duty applications like industrial containers.
- Chemical Resistance: Withstands acids, alkalis, and solvents, perfect for chemical storage tanks.
- Temperature Tolerance: Performs reliably from -50°C to 120°C, suitable for extreme environments.
- Moisture & UV Resistance: Waterproof and UV-stabilized grades ensure longevity in outdoor applications.
- FDA Compliance: Safe for food, pharmaceutical, and medical packaging, meeting stringent safety standards.
These properties make ZÜMRÜT’s HDPE a top choice for industries seeking durable, eco-friendly solutions from a reliable supplier of HDPE.
HDPE Grades We Supply
As a leading HDPE supplier, ZÜMRÜT offers specialized grades tailored to various manufacturing processes:
- Injection Molding Grade (Density: 0.952-0.958 g/cm³): Ideal for rigid products like bottle caps, automotive parts, and household goods. It’s fast molding cycle ensures cost-effective production.
- Blow Molding Grade (Density: 0.950-0.955 g/cm³): Perfect for hollow containers such as milk jugs, detergent bottles, and fuel tanks, offering uniform wall thickness.
- Extrusion Grade (Density: 0.945-0.960 g/cm³): Used for HDPE pipes, geomembranes, and films in construction and agriculture, ensuring leak-proof performance.
- High Molecular Weight HDPE (HMW-HDPE): Designed for abrasion-resistant liners and conveyor systems, ideal for heavy industrial use.
All grades comply with ASTM International standards, reinforcing our reputation as a top polyethylene supplier. check all grades(CLICK)
Applications of HDPE
ZÜMRÜT’s HDPE supports diverse industries, making us a versatile supplier of HDPE:
- Packaging: FDA-approved HDPE pellets for milk jugs, detergent containers, and food storage solutions.
- Construction: Corrosion-resistant HDPE pipes and geomembranes for water distribution and insulation.
- Automotive: Lightweight fuel tanks and battery casings for improved efficiency.
- Healthcare: Sterilizable medical devices and tamper-proof packaging.
- Agriculture: UV-resistant films and HDPE pipes for irrigation and greenhouse systems.
Our HDPE pipes, known for leak-proof joints and a 50+ year lifespan, are a cornerstone for infrastructure projects, reducing maintenance costs.
Benefits of Choosing ZÜMRÜT as Your Supplier of HDPE
Partnering with ZÜMRÜT, a global HDPE supplier, offers:
- Eco-Friendly Solutions: 100% recyclable HDPE (#2 resin code) supports circular economy goals, aligning with EPA recycling guidelines.
- Cost-Effective: Long service life minimizes replacement and maintenance costs.
- Durability: Resists cracking, chemicals, and environmental stress, ensuring reliability.
- Lightweight Design: Reduces transportation emissions, ideal for sustainable HDPE solutions.
- Recycled HDPE (rHDPE): Repurposed into furniture, fencing, and new packaging, promoting sustainability.
Our commitment to quality and sustainability makes ZÜMRÜT the go-to supplier of HDPE for businesses worldwide.
Packaging and Storage of HDPE Raw Materials
As a professional HDPE supplier, ZÜMRÜT ensures material integrity with industry-optimized packaging:
- Pellets: Supplied in 25-kg moisture-proof bags or bulk containers for injection molding.
Our logistics adhere to ISO 9001 standards, ensuring safe delivery to your facility.
Safety Guidelines for Handling HDPE
HDPE is non-toxic, but follow these precautions when working with materials from your supplier of HDPE:
- Ventilation: Ensure proper airflow during melting to disperse fumes.
- PPE: Wear heat-resistant gloves and safety goggles during processing.
- Storage: Keep HDPE away from ignition sources (flammable at 349°C).
- Recycling: Partner with certified recyclers per EPA guidelines for sustainable HDPE disposal.
Case Study: HDPE in Infrastructure Projects
In 2024, ZÜMRÜT, a leading supplier of HDPE, provided extrusion-grade HDPE pipes for a major water distribution project. Our pipes, with a 50-year lifespan, reduced leaks by 98% compared to traditional materials, saving 20% on maintenance costs. This project highlights our expertise as a polyethylene supplier for high-performance applications.
FAQs About HDPE
ZÜMRÜT delivers ASTM-compliant, sustainable HDPE with global delivery, tailored to your industry needs
HDPE remains ductile at -50°C and performs up to 120°C, making it versatile for various environments.
HDPE is denser and more rigid, ideal for pipes and containers, while LDPE is flexible. As a supplier of HDPE, we specialize in rigid, durable applications.
Yes, HDPE is 100% recyclable, making it an eco-friendly choice for businesses. As a leading supplier of HDPE, ZÜMRÜT International Kimya Co. provides sustainable HDPE materials with a #2 resin code, supporting circular economy goals. Our HDPE can be repurposed into products like furniture, fencing, and new packaging, aligning with EPA recycling guidelines. We partner with certified recyclers to ensure responsible disposal and minimal environmental impact.
Why Choose ZÜMRÜT as Your Supplier of HDPE?
As a trusted supplier of HDPE, ZÜMRÜT International Kimya Co. provides durable, eco-friendly HDPE solutions for packaging, construction, and more. Our commitment to quality, sustainability, and customer satisfaction sets us apart as a leading HDPE manufacturer and supplier. Explore our HDPE product catalog or learn more about HDPE recycling to see how we support your business goals.
Contact Us:
Ready to source premium HDPE? Contact ZÜMRÜT, your trusted supplier of HDPE, today. (CONTACT US)
- Email: info@causticsodaco.com
- WhatsApp: +971 50 720 9246
- Address: No. 2305, Burlington Tower, Business Bay, Dubai, UAE