The Role of Polyethylene Wax (PE WAX) in Cable Production
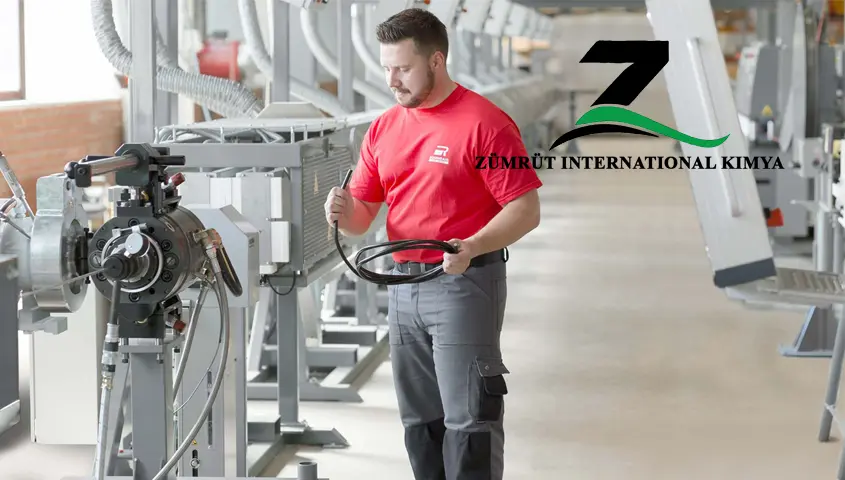
Introduction
Polyethylene wax is one of the important additives in the production of cables, with essential properties that enhance cable processing, performance, and durability. With growing demands for high-performance cables in a wide range of industries including telecommunications, power distribution, and electronics addition of PE wax into the products has become important to achieve these expectations. The article focuses on the important role that polyethylene wax plays in cable manufacturing, its benefits, and its applications.
What is Polyethylene Wax?
Polyethylene wax is a low-molecular-weight polyethylene polymer, also known as PE wax, which is famous for its excellent thermal stability, lubrication, and chemical resistance. This is a very versatile material used in many industries: plastics, rubber, coatings, and cable production. In the context of cable manufacturing, PE wax is considered a performance enhancer for the production process and the quality of the final product.
Applications of Polyethylene Wax in Cable Production
Lubrication for Efficient Cable Extrusion:
- Another key role of polyethylene wax in cable production is acting as a lubricant during the extrusion process. The material reduces friction between the polymer material and equipment, ensuring good material flow. This is not only in improving the rate of production but also in avoiding excessive heat build-up, which degrades the polymer material.
Enhanced Surface Finish:
- The main contribution of polyethylene wax to cables is the realization of a smooth and even surface. This is very important in ensuring proper insulation and protection, besides meeting aesthetic and performance standards in high-quality cables.
Uniform Dispersion of Additives:
- In cable production, a number of additives are used, including flame retardants, stabilizers, and pigments. Polyethylene wax ensures these additives are evenly dispersed within the polymer matrix, enhancing the functional properties of the cables while maintaining consistent color and appearance.
Improved Thermal Stability:
- Polyethylene wax is used to enhance the heat resistance of cable sheathing and insulation materials. In particular, cables experience such high temperatures both in production and during operation that their structural integrity and performance depend on it.
Moisture Resistance for Outdoor Applications:
- Cables are normally exposed to moisture and humidity, especially in outdoor and underground installations. Polyethylene wax improves the moisture resistance of the polymer by preventing water ingress that may cause the degradation of cables.
Compatibility with Cable Materials:
- PE wax is highly compatible with many polymer materials used in cable manufacturing, such as polyethylene, polypropylene, and PVC. This makes it a versatile additive in a wide range of cable production processes.
Key Benefits of PE Wax in Cable Manufacturing
- Increased Processing Efficiency:
By reducing friction and optimizing material flow during extrusion, polyethylene wax enhances production speed and reduces energy consumption. - Enhanced Mechanical Properties:
PE wax strengthens the polymer structure, improving the durability, flexibility, and resistance of cables to mechanical stress. - Cost-Effective Production:
The addition of PE wax reduces material wastage, extends the lifespan of production equipment by minimizing wear and tear, and ultimately lowers manufacturing costs. - Environmental Resistance:
Cables enhanced with polyethylene wax demonstrate superior resistance to environmental factors such as UV radiation, temperature fluctuations, and moisture, making them suitable for harsh conditions.
Types of PE Wax Used in Cable Production
Polyethylene wax is available in several grades and forms, each tailored to specific cable production needs:
- Low-Density Polyethylene (LDPE) Wax:
This type of PE wax is ideal for applications requiring flexibility and elasticity, often used in insulation and protective sheathing for cables. - High-Density Polyethylene (HDPE) Wax:
Known for its hardness and high-temperature resistance, HDPE wax is preferred in heavy-duty cable applications, such as industrial power cables. - Oxidized Polyethylene Wax (OPE Wax):
OPE wax offers additional properties such as enhanced compatibility with polar additives and improved adhesion, making it suitable for specialized cable coatings.
Environmental Considerations
Modern production of polyethylene wax is made in an eco-friendly manner. Most of the manufacturers are now producing PE wax with less environmental impact, joining the race of the whole world towards greener manufacturing processes. The use of polyethylene wax in cable production enhances product quality and supports eco-conscious industrial practices.
Why Polyethylene Wax is Essential for Modern Cable Production
Polyethylene wax is included during cable production not just out of convenience, but out of necessity. With its benefits in processing efficiency, durability, and superior surface finishes, it becomes one important component in creating cables that answer today’s most onerous demands for modern industries. Besides, this ensures its versatility and applicability with a wide range of polymers in different cable production conditions.
Conclusion
Polyethylene wax is among the key materials in cable production, offering unparalleled processing, performance, and product longevity. From lubrication and thermal stability to moisture resistance and additive dispersion, PE wax ensures that cables meet the highest standard of quality and reliability.
For cable-grade, high-quality polyethylene wax, ZÜMRÜT International Kimya Co. offers premium solutions. Contact us today.